About the Company History and the Present
1993 - 1996
The beginnings of the company date back to 23 January 1993, when we made our first order in the garage of the family house. It was the casting of rocker arms for the automotive industry. Due to increasing orders, we established Strojírny Kohout in 1996 with the intention of finishing castings in large quantities and developing new technologies for the local foundry.
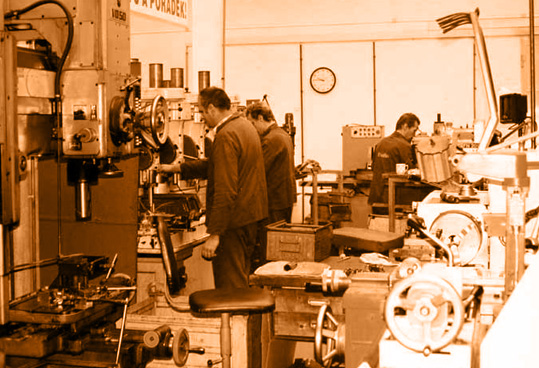
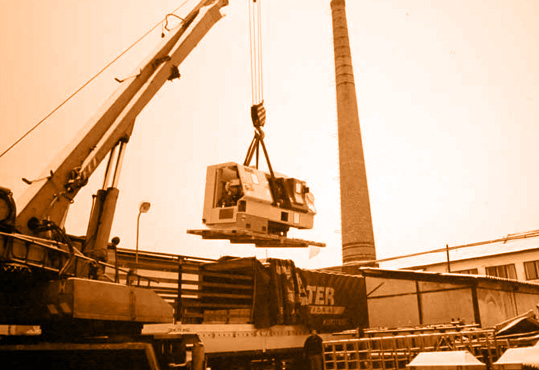
1996 - 2001
Between 1996 and 2001, the company experienced growth in both orders and the number of employees. The main order during this period was the large-scale finishing of castings for a local foundry.
In 2001, we set another direction for the development of the company, namely custom machining on CNC machines for companies operating in the humane industries. We purchased our first CNC lathes from Mazak and offered our customers the new technology. Cooperation with several Czech companies and a Swiss company engaged in the manufacture of cable cars began.
2003 - 2007
After 2003, we managed to expand into foreign markets and established cooperation with a number of foreign companies. This laid the foundation for today's orientation in contract manufacturing. More and more companies from Germany were able to become customers, which are still the most important pillar of Kohout today.
Thanks to this development, in 2003 the first CNC milling machine was purchased, again from Mazak, and this type of machining was included in the production program. The Kohout company thus grew to approximately 80 employees. Subsequently, other CNC machines were purchased, such as a Mazak shuttle milling machine that can work on two sides.
The year 2007 was marked by a significant decrease in orders in the area of machining and finishing of castings for a local foundry. Thanks to a strategic decision in 2001 and a good team of people, we replaced this loss with other orders.
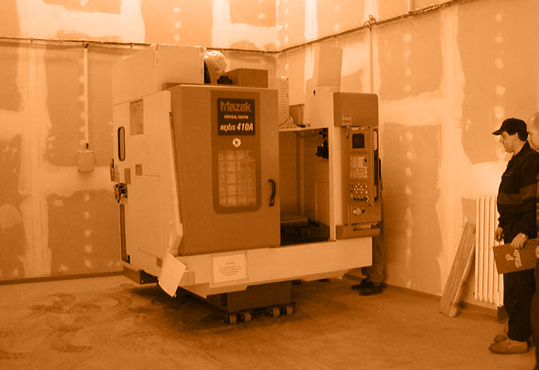
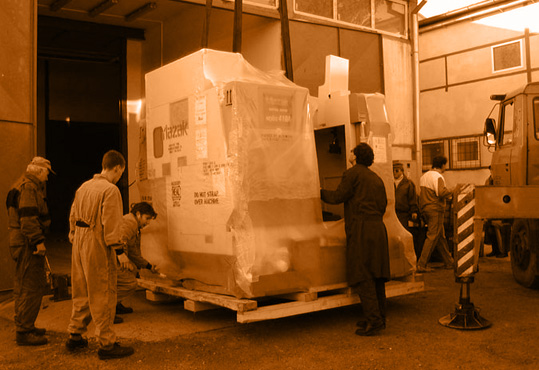
2010 - 2013
Between 2010 and 2013, we focused on intensive development of the company, including the optimization of internal processes. We invested in the reconstruction of production facilities, infrastructure, and new multi-axis machining technologies. We offered our leading CNC machine operators positions in production preparation, which significantly increased manufacturing productivity.
We also expanded our sales team, which is actively in touch with all customers.
2014 - 2016
In 2014, we purchased two new MAZAK CNC machines (lathe and milling), reconstructed sanitary facilities for our employees, completely reconstructed the in-house computer network (with fiber optic cables), and modernized the camera and security system. We also began the reconstruction of the last part of the production hall. At the end of the year, a tender for a supplier of a 5-axis milling machining centre was held.
In 2015 - 2016 we continued the reconstruction of other production facilities, we purchased new machines - 5-axis milling centre HERMLE C42 (2015), turning centre Mazak Hyperquadrex HQR 200 MSY (2016).
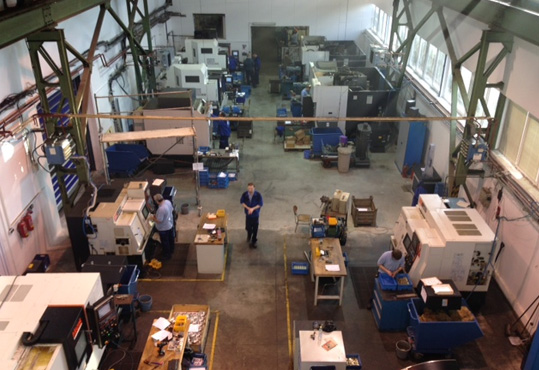
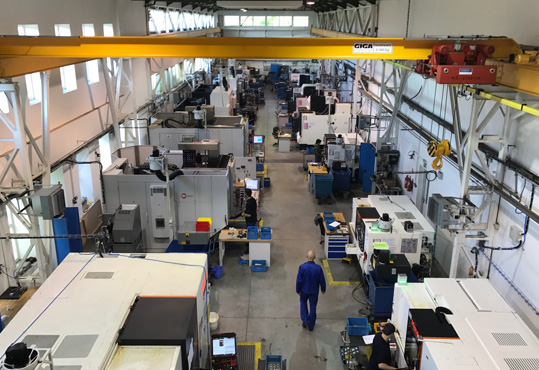
2017
In 2017, we renovated our office space, purchased a HERMLE C32 5-axis milling centre and a Mazak QT 200M lathe. Due to a significant increase in orders, we intensified our partnerships with cooperating companies performing surface treatments for us.
In this year we also launched a scholarship programme for selected students from the Secondary Vocational school in Domažlice.
2018
In January 2018 we purchased a Brother RX450 CNC milling machine with automated workpiece clamping and another Hermle 5-axis milling centre with HS flex automated handling system.
Due to the successful launch of the project to support vocational school students through scholarships, we decided to increase the number of supported students from 4 to 8.
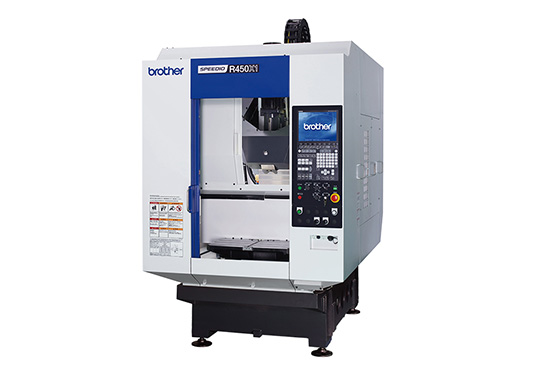
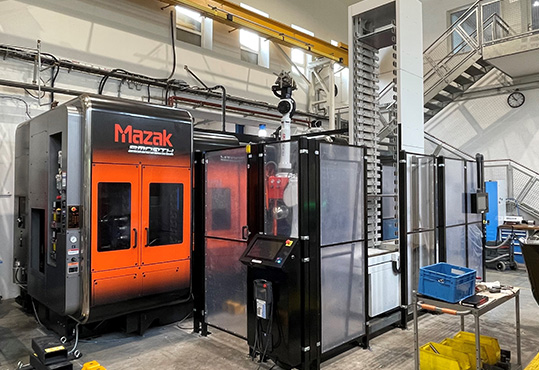
2020 - 2022
2021 - Installation of the new MAZAK Integrex I200ST machining centre. This is a unique machine configuration in the Czech Republic, as this equipment is one of the most modern turning and milling machines currently available on the market. It enables the production of gearing using the PowerSkiving method and is equipped with the ROBOJOB TOWER robotic workstation for unattended machining and Renishaw and Blum measuring systems. The acquisition of this centre was the largest single investment the company had ever made.